-
- News
- Books
Featured Books
- pcb007 Magazine
Latest Issues
Current IssueAlternate Metallization Processes
Traditional electroless copper and electroless copper immersion gold have been primary PCB plating methods for decades. But alternative plating metals and processes have been introduced over the past few years as miniaturization and advanced packaging continue to develop.
Technology Roadmaps
In this issue of PCB007 Magazine, we discuss technology roadmaps and what they mean for our businesses, providing context to the all-important question: What is my company’s technology roadmap?
Wet Process Control
In this issue, we examine wet processes and how to obtain a better degree of control that allows usable data to guide our decisions and produce consistently higher-quality products.
- Articles
- Columns
Search Console
- Links
- Media kit
||| MENU - pcb007 Magazine
Estimated reading time: 8 minutes
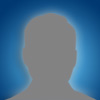
Contact Columnist Form
The Bleeding Edge: Designing Microelectronic Printed Circuits
By Robert Tarzwell with Ken Bahl - Sierra Proto ExpressThe world of electronics is about to explode or, should I say "implode," the definition of which is "to collapse inward, violently." This implosion will be driven by a serious size reduction or, huge improvements in the functionality of electronic products, resulting in the miniaturization of the printed circuit board. Today, the size reduction in the basic circuit board will allow designers to reduce the size of their PCBs by half or, to a quarter, the original size. We say "today," because, as of this writing, I know of a few companies moving into microelectronic printed circuits; the very fine lines that used to be unavailable to the designers will now become mainstream, with the old absolute minimum line width of 75 microns (3 mils) giving way to 30 microns (1.2 mil ) or less.
With smaller traces and vias, new design rules are required because the printed circuit manufacturing methods are quite different and advanced. Micro electronic printed circuit manufacturers are unable to use the standard old dryfilm, plate and etch process to make lines under 75 microns reliably. Photolithography is the method of choice to generate these very fine lines and spaces. The move to smaller line widths may catch quite a few "stuck-in-the-mud" old fashioned printed circuit fabricators off guard who do not even offer 3 mil now. To be competitive in the very near future the PCB shops will need to be offering at least 50 micron lines and spaces or even down to 30.
The manufacturers of fine microcircuits are divided into four groups. Group One is mostly Asian with one or two USA captive high volume electronic manufacturers that have developed a unique fine-line process of 40-50 micron traces for their cell phones or their ipods. Group Two is a very limited number of research and development companies manufacturing a small number of very specialized circuits with very fine-lines under 40 microns built only on Kapton where costs are high and delivery times are three months long and production quantities are small. Group Three is expanding the fastest with mid-sized printed circuit companies offering smaller production numbers with line widths of 75 to 40 microns and production quantities in the thousands with a couple week turn around. The last, Group Four is normal fine line printed circuit production of 125 to 75 microns with high volume and many players. We place ourselves (Sierra Microelectronics) in the Fifth Group. We have developed a new manufacturing technology capable of 30 micron lines and spaces on FR4 or Kapton. We also have
As the business of microelectronics expands and more printed circuit companies find the technology necessary to manufacture very fine lines of 40 micron and below, the Designers will need to become familiar with the new design rules as well as microcircuit manufacturing advantages and shortcomings
Very fine lines of 30 microns cannot, for obvious reasons, use normal one ounce copper. As we reduce the line width we must reduce the thickness. At Sierra we have manufactured 25 micron lines using 18 micron thick copper but that would be about the upper limit. Thinner copper traces should not be a problem unless your design uses higher current, in which case the specific trace can be made wider to handle the higher current. A 30 micron line is tough and reliable, however it cannot take a lot of physical abuse which can be nearly eliminated through the use of a typical soldermask. The fine traces may concern many designers, however, they need to realize the 200 micron wide trace they currently start with reduces down to a 25 to 13 micron aluminum or gold round wire which connects the die to the chip carrier. The fine lines are encapsulated either in the inner layers of the multilayer or by Soldermask which means they are virtually locked in. New methods of adhering copper to the circuit board surface have been developed and are used to improve the overall adhesion of a micro trace to the surface. We have a sample board with 40 micron traces without solder mask which we allow customers to scratch at with their finger nails. So far, no one has dislodged a trace.
The first few micro designs had big fillets from the 30 micron trace to the pad. Over time, it has proven unnecessary; routing the trace direct to the pad is very strong and reliable. The extra fillets have just proven to increase image writing time and costs.
Small vias: there is a physical limit to the size of microvias. Below 50 microns (2 mils) the plating solution will not properly plate the hole wall, resulting in poor via quality. Our laser can drill holes as small as 20 microns, but we can't plate them. The thickness of the laminate controls the minimum diameter of the vias, with an upper limit of 2:1 for plating micro-vias. For example, a three-mil microvia is limited to a six-mil thick laminate with respect to plating. There is also a limit of how deep our Yag laser can drill a via. As the diameter decreases so does the ability to penetrate the laminate for a clean hole. A three-mil via is limited to a four to five mils depth in FR4 and six to seven mils in a glass free laminate used in HDI applications. All about the microvia is not necessarily bad. The microvia may not be able to be as small as the traces, but we can add a sweetener to the pot since the annular ring around the microvia can be significantly smaller.
The first thing we noticed when we produced our very first micro PCB was that the vias were dead center in the pad. The design used a nine-mil pad and a three-mil via which is tight for conventional printed circuit engineering. The new, more accurate laser manufacturing method would allow as small as a five-mil pad with a three-mil via, thus saving an enormous amount of board area.
Picture of a nine-mil pad and a three-mil via with 40 micron lines
Utilizing new micro circuit design technology instead of the normal printed circuit technology results in significant real estate savings. The best pitch available today with typical 75 micron line widths is approximately .5mm resulting in a 75 micron (3 mil) via with 75 micron lines and a 250 micron (10 mil ) pad. The space between the pads is 225 microns (9 mils ) allowing only one 75 micron line between pads and this minimum specification is tough for most shops.
Very Fine TechnologyMicro circuit technology
Micro circuit technology utilizing a three-mil via, a five-mil, a 30 micron line and 30 micron spaces, results in a .2mm pitch layout.
When compared to a standard three-mil printed circuit board layout, the microcircuit technology results in a five-fold reduction in area used. In future articles, we will cover ideas to reduce component area required. However, even with the same components, just switching to 30 micron lines and smaller pads will significantly reduce the board area.
When you route the lines use the same technique but try to angle lines when turning a corner rather then using a single 90 degree turn. The angled lines around the corner spreads the corner stress over a wider area.
Avoid Okay
Microvias
When utilizing HDI technology layers added on top of a multilayer board or as an all HDI multilayer, microvia's are used to connect between the thin layers. Through-holes can be drilled 5.9 mils in diameter up to 60 mils thick or laser drilled holes 2-3 mils in diameter but only in 2-4 mils thick HDI laminate. Keep in mind that drilled holes wander greatly compared to laser created holes which limits the size of the pad to hole. For drilled holes use a 12-mil pad with a six-mil hole, whereas for a laser drilled microvia a five-mil pad can be used with a three-mil via.
Copper thickness
Normal three-mil fine-line circuitry is 1 oz of copper, microcircuits use oz per 30 microns width. Normal pattern plating is used in the manufacture of micro circuits which means the traces do not have to exit the circuit to a plating buss line, pattern plating connects to the entire circuit and wire bonding plating is electroless or electrical.
Reliability
Most normal printed circuit laminates can be used for HDI or microcircuits but all have limitations. Micro single and double sided circuits can be manufactured out of rigid FR4 type laminates however they need to be thin to allow for micro through-holes.
Electrical testing
The lower limit of flying probe or even rigid probe (bed of nails) technology is at 2-3 mil pitch right now We expect it to lower over time as necessity requires smaller landing pads. If your micro circuit has smaller points such as edge strip connectors, it is wise to extend the lines off the circuit to a 3-4 mil pad.
Soldermask
The imaging improvements that allow us to manufacture 30 micron lines, unfortunately, has not been transferred to soldermask. 75 micron position accuracy as well as image resolution is still the limit.
Identification marking
Typical silkscreen image accuracy is too large for microcircuits. Sierra Proto utilizes a very fine ink jet printer, which results in a significantly small Identification marking resolution.
Security marking
Very small individual bar codes can be imaged into the solder mask to positively identify the printed circuit board. Bar codes can be so small they are virtually invisible to the human eye.
8 micron security bar code
R&D mil 15 micron line
Final finish
Normal printed circuit finishes are available. Most microcircuits use wire bondable soft gold, Immersion tin or silver.
New technology
The Sierra Micro Electronics research department is working on the future with nano printed circuits as well as high thermally conductive micro circuits on copper or aluminum. Stay tuned!
inch square micro chip carrier
Robert Tarzwell Director of Technology Sierra Proto Express
Ken Bahl CEO Sierra Proto Express For more information, visit: http://www.protoexpress.com/
More Columns from Various Archived Columns
Slash Sheet Chaos: Is What You See, What You Get?Moisture in Materials: Avoiding Process Gremlins
Material Witness: Beat the Heat--A Non-Math Intro to Thermal Properties
Material Witness: Considerations in Using TC Materials for PWBs
Material Witness: Are Your Materials Up to the Challenge?
Material Witness: Thermal Oxidation of Materials, Part I
Material Witness: Thermal Oxidation of Materials, Part II
Material Witness: R.I.P. Speedboard C